CO2排出量削減のカギはサメ肌技術にあり ANAの新たな挑戦
「ついに、ついにここまで来たんだな……」
2024年9月2日。成田空港の駐機スポットに立った松井宏司朗は、胸の内でこうつぶやいていた。視線の先にあったのは、ボーイング777型機のフレイター(貨物専用機)。一見、ごく普通のフレイターのようだが、松井がまじまじと見つめる機体の“胴体部分”、その表面には、ある特殊なフィルムが装着されていた。この日は、その新技術を実装した初号機が、初めてのフライトを迎えたのだ。
ANAグループは「航空機の運航で発生するCO2排出量を、2050年度までに実質ゼロにする」という長期環境目標を掲げている。離陸の際、早い段階で翼のフラップを戻して空気抵抗を抑える「Normal Climb」。着陸時、逆噴射装置(リバーサー)の出力を小さくして燃料消費量を抑制する「Reverse Idle」。着陸後に一つのエンジンだけで地上を走行する「One Engine Taxi In」――。これら運航上の3大施策にANAは長年取り組んできたほか、バイオマスや廃食油、排ガスなど循環型の原料から製造される「SAF(Sustainable Aviation Fuel=持続可能な航空燃料)」をいち早く導入したのも、目標達成に向けた一環だった。
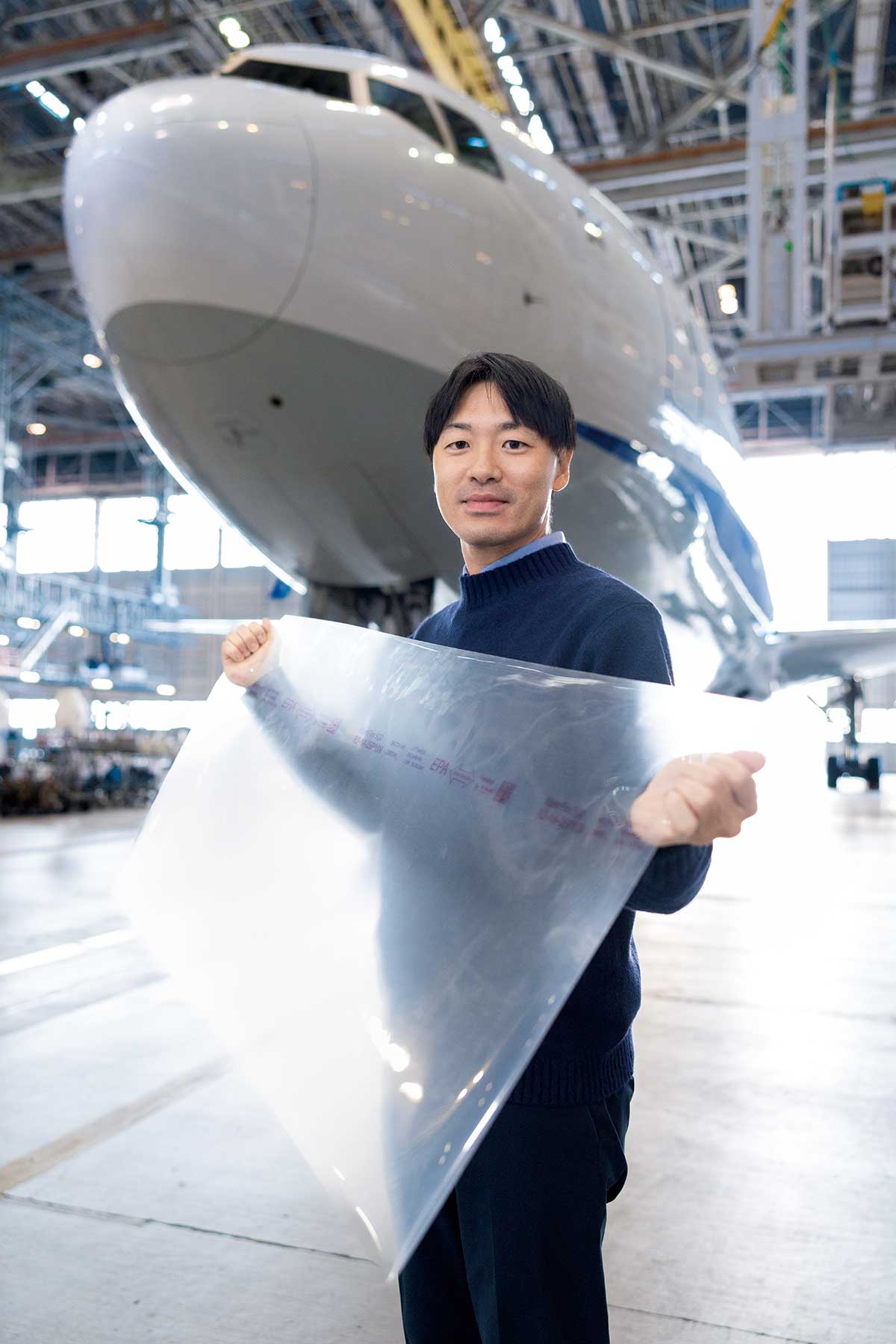
そして、整備センター技術部・構造技術チームの松井がこの数年、携わってきたのが“サメ肌”をモチーフとしたリブレット加工フィルム、「AeroSHARK」の実装だったのだ。サメのざらざらとした表皮は、水中の摩擦抵抗を低減、より少ない力で泳ぐことを可能にしている。そのサメ肌を生体模倣したフィルムを機体表面に貼り付けることで、エネルギー効率を上げることが可能となる。AeroSHARKをドイツの総合化学会社であるBASFと共同開発したルフトハンザ・テクニックの試算によれば、1機あたりで年間最大、約250トンの燃料消費量と、800トンものCO2排出量の削減が期待できるという。
「でも、当初は私自身、半信半疑で……」と松井は苦笑いを浮かべ、言葉を続けた。「昔、オリンピックで活躍した競泳のイアン・ソープ選手が、サメ肌の水着を着用して好成績を残したことは、私も記憶にあります。でも、AeroSHARKの加工幅は50マイクロメートル(1000分の50ミリ)と、髪の毛ほど、ごく微かな山と谷が作られているだけ。その薄いフィルムに初めて触れたときは『本当にこれで、そんなにCO2を削減できるのか!?』というのが、正直な感想でした。とはいえ、私も環境問題にはもともと興味がありましたし、CO2排出量の削減は喫緊(きっきん)の課題だということも、もちろん理解していましたから。少しでも可能性があることなら、ぜひ取り組んでみたい、そう強く思いスタートしました」
ただし……、創業以来、安全運航を第一義としてきたANAにとって、いくらCO2排出量の削減効果をうたっているとはいえ、新たな機能を飛行機に付与するというのは、決して簡単に進められることではなかった。
「装着したことで、もしなにかがあった場合は、いったいどう対処するのか。起こりうる事象、そのすべてを事前に想定し、準備をしていくというのは、当初考えていた以上にたいへんな作業でした」今回の「翼の流儀」では、改修2号機目が、国際線の旅客便に就航予定(2025年4月下旬以降)となるなど、大きな期待を背負う新技術と、その導入に尽力した技術者の思いを紹介する。
空気抵抗を減らすために微細な凸凹を表面につくる
2008年、松井はANAに入社した。「大学時代、設計やデザインなど、ものづくりを学びました。また、乗り物も好きでした。だから、好きな乗り物のそばで、手を動かして仕事ができる環境に身を置きたいと。それが志望動機でした」入社後、4年間は整備士として勤務。5年目からは現在、籍を置く技術部に。
「機体構造に発生するような不具合の技術対策を検討したり、手順書を作成するという部署。構造という意味では、ペイントなど機体の表面処理も担当の一つで、その一環として3年ほど前から、リブレットの技術に関わり始めました」
ANAでは2022年、当初はニコンが開発したリブレットフィルムを機体に小さく、部分的に貼り付け、耐久性などの技術評価を始めていた。
「ニコンさんの技術に問題はないのですが、認証等のハードルが高く、すぐに本格的な導入をすることは叶いません。それにはまだ少し、時間が必要でした。しかし、CO2の排出量削減は待ったなしの状況です。すぐにでも実装できる技術はないかと探し求め、ルフトハンザ・テクニックと、BASFが共同開発したAeroSHARKが、すでにヨーロッパの航空局の認証を得ていることがわかりました。こうして、先方にコンタクトを取ったのが2023年でした」
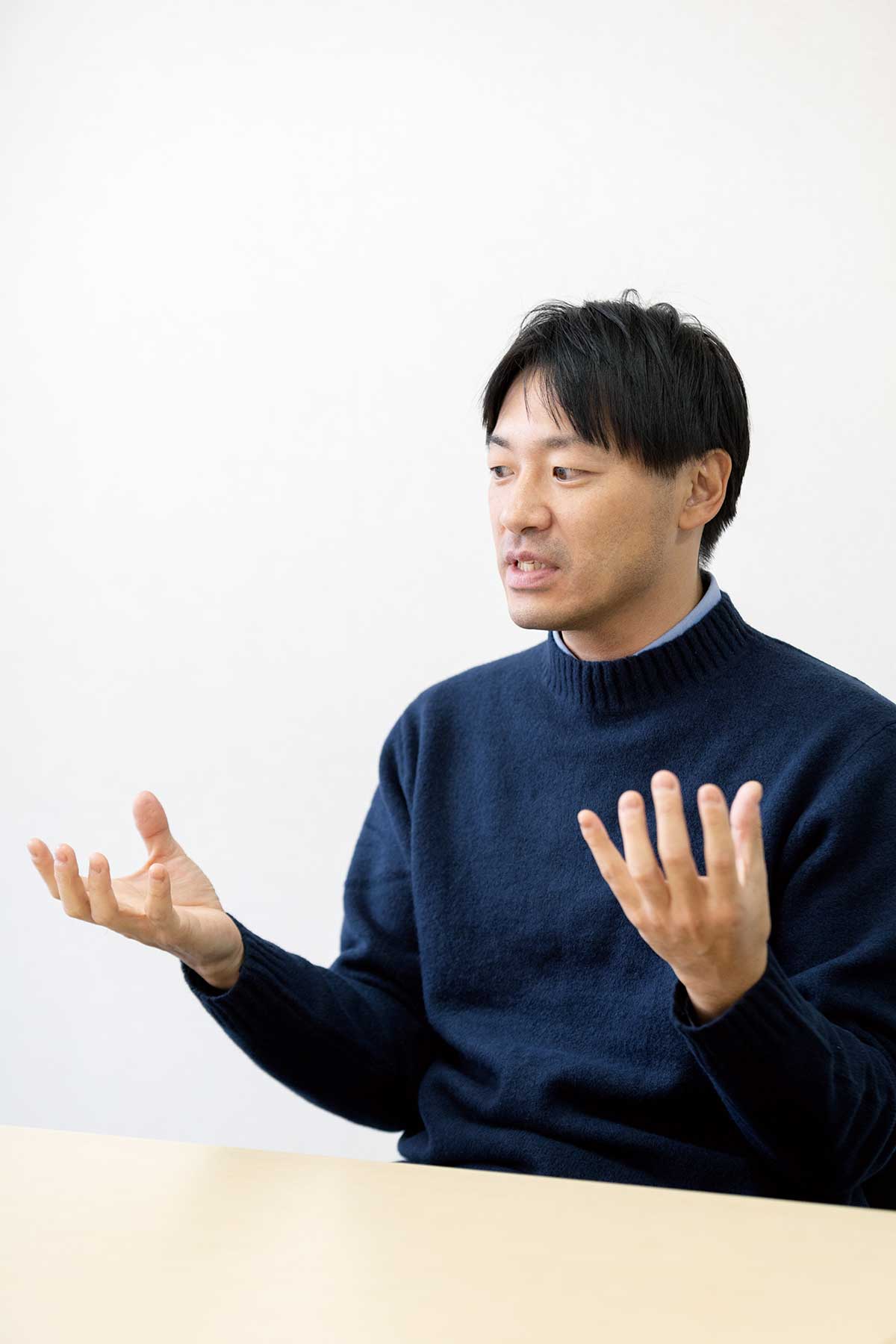
「今月、改修2号機目が国際線の旅客便に就航する予定です。ご搭乗の際、もしかしたらフィルムを視認していただけるかもしれません」(松井)
フィリピンにあるルフトハンザ・テクニックの改修工場を訪問。松井はそこで初めて、AeroSHARKの実物に触れた。
「近年、流体力学的には、表面に微細な突起や溝を刻むことで乱流摩擦抵抗が大きく低減されることが広く知られています。かつて空気抵抗が少ないと考えられていた滑らかでツルッとした表面では、逆に空気と物体の間に抵抗となる渦が発生してしまう。その点、リブレット加工が施されていると、空気が凸凹の、凸の頂点に当たり、相対的に発生する渦が減少、結果的に抵抗も減って、それだけエネルギー効率も上がり、少ない燃料で飛ぶことが可能になるんです。ひいては、排出されるCO2の量も減る――これがリブレット加工フィルムの原理と、その効果です」
先に松井はその例として、かつて一世を風靡した競泳水着を挙げたが、いまやサメ肌は、風力発電のブレードや、F1マシンのウイング、もっと身近なところでは、エアコンの室外機のファンや、家電のモーターのブレードなど、多くの場所で実用化に向けた取り組みが行われているという。ルフトハンザ・テクニックとの交渉を重ね、導入が近づいた新技術。だが、まだ越えなければならないハードルが、じつはANAの社内に残されていた。
新技術導入に向けさまざまなリスクに対応
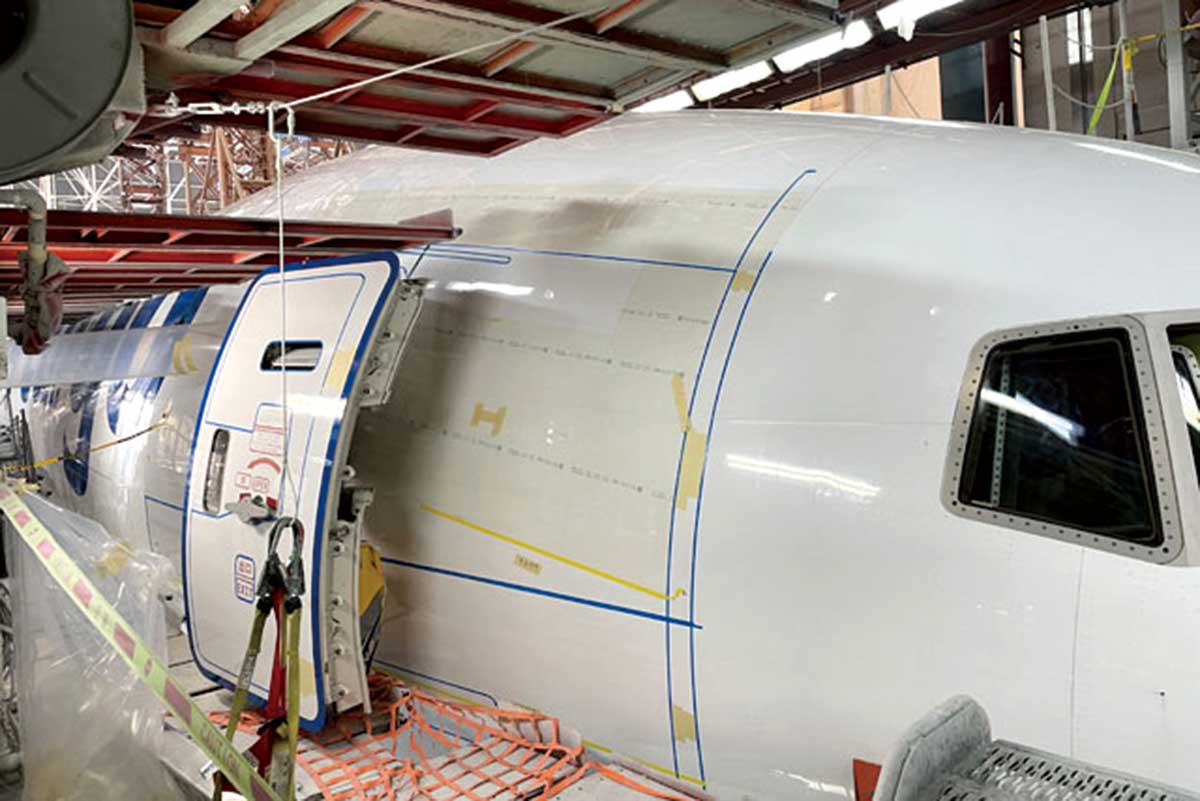
「もっともたいへんだったことは……、それこそ本来、機体になかったものを、改めて搭載する、装着する、それ自体が最大のハードルでした」
松井はこう言って振り返った。そう、安全・安心のフライトに専心してきた者たちにとって、従来、なんら問題なく安全に飛ばしてきた飛行機に、さらに新しいものを加えるということへの抵抗感は、並大抵のものではなかったのだ。
「整備の面からは『破損など、装着したフィルム自体になにかあった際、どう対処するのか?』『フィルムの下の構造物に不具合があったとき、このフィルムの取り扱いはどうすればいいのか?』などなど、不安な点や疑問を数多く突きつけられました。また、飛行機からの落下物というのは大問題ですから、そういった懸念が持ち上がることは当初から念頭にあって。認証を持つルフトハンザ・テクニックに、飛行中に剥離しないことを再三確認しました」
同僚たちの抱いた疑問はまだまだあった。「実装機の就航後、いつまでに貼り替えるのか。その際はどうやって改修を行うか。機体洗浄の方法に違いはあるのか。燃費が向上するフィルムがもし劣化等によって、その効果が低減した場合、どう対処すればいいのか。その際はどこの部署間で連絡を取り合うのか。そういった取り決めはきちんとできているのか……。あらかじめ自分でも数多のリスクを想定し、また、関連する多くの部署からも前向きに『こんなケースは?』と疑問を投げかけてもらいました」
結果的に松井は60以上のリスクを洗い出し、すべての対処方法を準備して、導入に至った。昨年8月。AeroSHARKを実装するための、ボーイング777型機の改修が、中国・アモイの整備工場で行われた。
「1メートル×50センチのフィルムを一枚ずつ、手作業で貼っています。事前にルフトハンザ・テクニックの担当者を呼んで、貼り方のレクチャーを受けています。機体の胴体部分、その7割ほどの面積に貼っています。翼やエンジンカウル、それにコックピット周辺や機体天井エリアには、作業面も考慮し、貼ってはいません」
こうして迎えた9月2日。初号機が成田空港でお披露目された。「感動したのは、そこで、改修後の機体と対面したときです。私は改修作業の途中で帰国していたので、完成した機体を初めて目の当たりに。とてもキレイに仕上がっていて『やっとここまで辿り着くことができたんだな』と、胸が熱くなりました」
一つの仕事を完遂した感動に打ち震える思いを抱いたという松井。しかし、松井がそんな熱くなった胸を撫で下ろすことができたのは、それから数カ月後のことだった。
「去年の12月に、フライトオペレーション部門から、データをもらいました。それを見ると、初号機は想定したとおり、およそ1%の改善効果が確認できました。わずか1%ではありますが、年間にすると約250トンの燃料消費量と、800トンものCO2排出量の削減に繋がったことになります」
会社にはもちろん、地球環境への貢献という大きな役目を果たすことができた松井。撫で下ろしたばかりのはずが、今度はどこか、強く胸を張る若き技術者の姿が、そこにはあった。
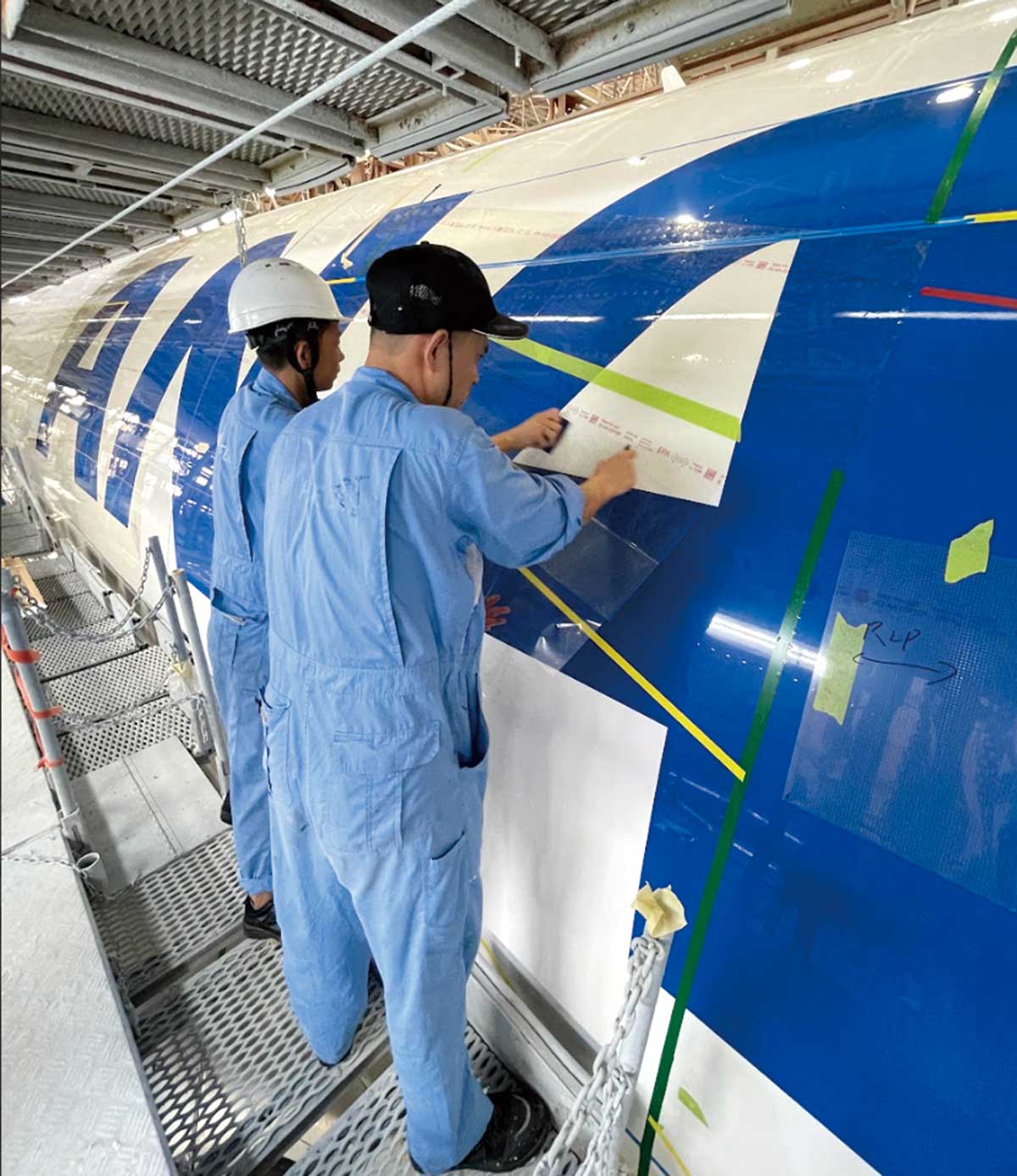
翼の王国のアンケートにぜひご協力ください。
抽選で当選した方にプレゼントを差し上げます。